Plate Heat Exchangers
BENEFITS
Plate heat exchangers (PHEs) offer several advantages, particularly when handling low-viscosity fluids without particles.
PRODUCTS
Plate Heat Exchangers, Brazed
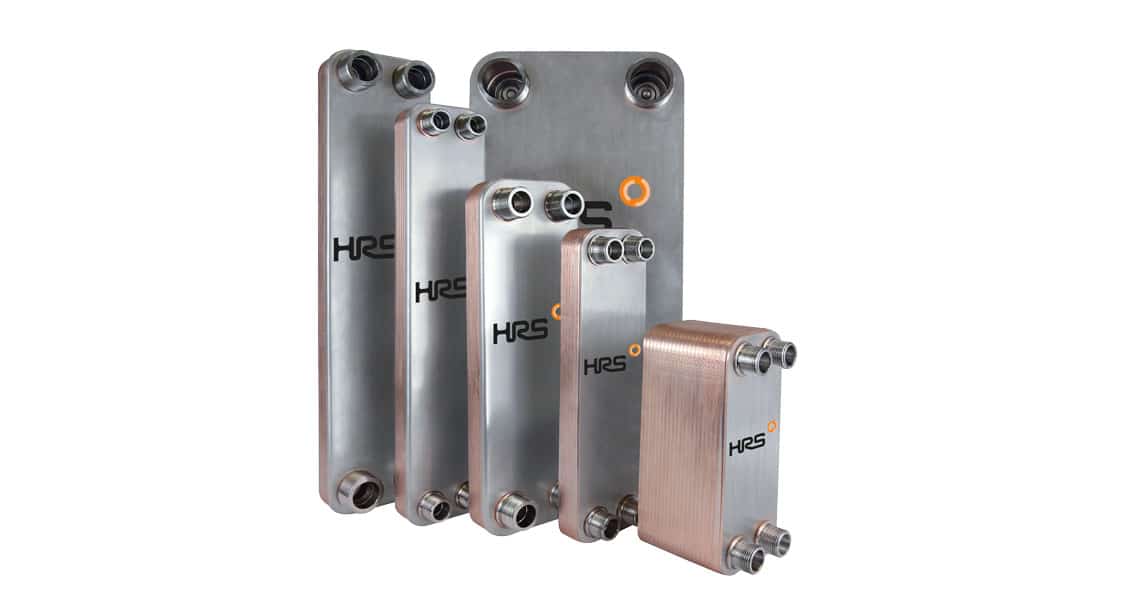
The HRS Brazed Plate Heat Exchanger range works on the same principle as conventional plate heat exchangers, but consists of a pack of corrugated plates joined together and sealed by furnace brazing. ...
FAQ
Plate heat exchangers consist of thin, corrugated plates assembled within a frame. The product flows through alternate channels, while the service fluid passes through the intervening channels. This arrangement facilitates efficient heat transfer between the two fluids without direct contact.
HRS provides two main types of plate heat exchangers:
- Gasketed Plate Heat Exchangers: These feature glueless clip gaskets for easy maintenance and are suitable for applications such as heating, cooling, pasteurising, and sterilising in the food and dairy industries.
- Brazed Plate Heat Exchangers: These consist of corrugated plates sealed by furnace brazing, offering a compact and efficient solution for various heat recovery applications.
HRS gasketed plate heat exchangers are typically manufactured from AISI 304/316 stainless steel or titanium, with plate thickness options of 0.6mm, 0.8mm, or 1.0mm. The frames are constructed from painted carbon steel, and the units are fitted with EPDM or NBR gaskets.
Plate heat exchangers offer several benefits, including:
- High Heat Transfer Efficiency: The corrugated plate design induces turbulence, enhancing the heat transfer coefficient.
- Compact Design: Their structure allows for a high surface area in a relatively small footprint.
- Flexibility: The modular design enables customisation to specific process requirements.
- Ease of Maintenance: Gasketed models allow for straightforward disassembly and cleaning.
HRS plate heat exchangers are utilised across various industries, including:
- Food & Beverage: For processes like pasteurisation, sterilisation, and cooling.
- Pharmaceutical: For heating and cooling processes requiring strict hygiene standards.
- Industrial: In sectors like petrochemicals and fine chemicals for efficient heat recovery.